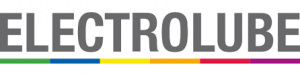
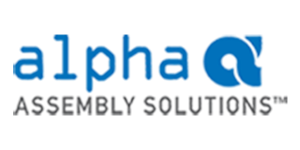
Conformal coating is a special polymeric film forming product that protects circuit boards, components, and other electronic devices from adverse environmental conditions. These coatings ‘conform’ to inherent irregularities in both the structure and environment of the PCB. They provide increased dielectric resistance, operational integrity, and protection from corrosive atmospheres, humidity, heat, fungus, and airborne contamination such as dirt and dust.
The following categories are based on the basic resin of each coating. The chemical composition of each conformal coating determines its major attributes and functions. Choosing the proper conformal coating for your application is determined by the operational requirements of your electronics.
- Acrylic Resin (AR) – Acrylic conformal coating provides fair elasticity and general protection. Acrylic conformal coating is recognized for its high dielectric strength, and fair moisture and abrasion resistance. What generally distinguishes acrylic coating from other resins is its facility for removal. Acrylic coatings are easily and quickly removed by a variety of solvents, often without requiring agitation. This makes rework and even field repair very practical and economical. On the other hand, acrylic coatings do not protect against solvents and solvent vapors, which could result in less than ideal performance for an application that involves something like pumping equipment. Acrylic coatings can be considered basic, entry-level protection, because they are economical and protect against a broad-level of contamination. However, they are not the best-in-class for any characteristic except possibly dielectric strength.
- Silicone Resin (SR) – Silicone conformal coating provides excellent protection in a very wide temperature range. SR provides good chemical resistance, moisture, and salt spray resistance, and is very flexible. Silicone conformal coating isn’t abrasion resistant because of its rubbery nature, but this property does make it resilient against vibrational stresses. Silicone coatings are commonly used in high-humidity environments. Special formulations that can coat LED lights without color shift or reduction of intensity are available, and make SR conformal coatings a popular choice for applications such as outdoor signs. Removal can be challenging, requiring specialized solvents, long soak time, and agitation from a brush or an ultrasonic bath.
- Urethane (Polyurethane) Resin (UR) – Urethane conformal coating is known for its excellent moisture and chemical resistance. It is also very abrasion resistant. Combining those factors with its solvent resistance results in a conformal coating that is very difficult to remove. Like silicone, full removal generally requires special solvents, long soak time, and agitation with a brush or an ultrasonic bath. Urethane conformal coating is commonly specified for aerospace applications where exposure to fuel vapors is a common concern.
The rest of this article is concerned mainly with what we call “traditional” conformal coatings, but we’ll first cover other coating types to provide a complete picture of the options available.
- Epoxy Conformal Coating – Epoxy resins (ER) are usually available as two‐part compounds and create a very hard coating. Epoxy conformal coatings provide very good humidity resistance and are not generally permeable, unlike traditional conformal coatings. They also have high abrasion and chemical resistance. Typically, they are very difficult to remove once cured and are not as flexible as the other materials. Epoxy coatings are common in potting compounds, which in contrast to conformal coatings, completely cover the electronics in a solid and level layer of material.
- Parylene Conformal Coating – Parylene conformal coatings are a unique type of coating applied by vapor phase deposition. They provide excellent dielectric strength and superior resistance to moisture, solvents, and extreme temperatures. Because of the vapor deposition method, parylene coatings can be applied thinly and still provide excellent circuit board protection. However, removal for rework is very difficult, requiring abrasion techniques, and without access to vapor phase deposition equipment, recoating with parylene is impossible.
- Thin Film /“Nano” Coatings – A coating is dissolved in a fluorocarbon‐based carrier solvent and applied with a spray or dip method to create a very thin coat, although not at a nanometer scale as the nickname suggests. They are commonly used to provide a minimal amount of hydrophobicity, which may prevent losses from very quick exposure to water. This type of coating does not offer the level of surface protection that other coating methods do.